Textile waste is a major environmental problem, as millions of tons of used clothing and other textiles end up in landfills or incinerators every year. Cotton, one of the most widely used natural fibers, has a high environmental impact due to its intensive water and chemical use during cultivation and processing. To reduce the textile industry’s footprint and promote a circular economy, new technologies for chemical recycling of cotton waste are emerging.
Chemical recycling involves dissolving the cotton fibers and regenerating them into new fibers that can be used for various applications. This article reviews some of the technologies for chemical recycling of cotton waste, such as NuCycl by Evrnu, Circulose by Renewcell, Ioncell by Aalto, Refibra by Lenzing, Saxcell, and Infinited Fiber. It also compares their advantages and limitations from technical, environmental, and economic perspectives.
NuCycl by Evrnu
Evrnu’s NuCycl technology is a fiber regeneration process that converts cotton-rich textile waste into new fiber that can be reformed again and again. Here is how the technology works:
- Collect, sort, and shred textile waste: The cycle starts with used cotton-rich textiles and production waste, which Evrnu works with textile recyclers, brands, and retailers to source. The textile waste is then collected, sorted, and shredded into small pieces.
- Liquify/purify into liquid pulp: The shredded textile waste is then liquified and purified into a liquid pulp using a proprietary blend of renewable chemicals. This process removes impurities and separates the cotton from other materials.
- Transform into Nucycl lyocell fiber: The liquid pulp is then transformed into Nucycl lyocell fiber, which looks and performs the same as, if not better than, virgin fiber. This fiber can be recycled again and again to make new products over and over.
The claimed positive points of NuCycl technology are:
- It provides a real alternative to high impact raw materials like cotton and polyester.
- Nucycl lyocell fiber can be transformed into a range of applications, from casual apparel to footwear to home textiles.
- The fiber is equal to or stronger than the virgin cotton it can replace.
- It can be recycled up to 5x.
The limitations of NuCycl technology are:
- The chemical recycling process can be costly and often energy-intensive.
- The technology is still in the early stages of development and is not yet widely available.
- The process involves the use of a proprietary blend of renewable chemicals, which may not be sustainable or environmentally friendly.
- There are extra costs included in pre-processing which comprises of washing, opening, separation process, removal of contaminations, decolour, etc.
Overall, NuCycl technology is a promising solution to the textile waste crisis, but it also has its limitations. The choice of chemicals and the conditions of the recycling process can impact the efficiency and environmental impact of the process.
Circulose® by Renewcell
Renewcell technology is a chemical recycling process that dissolves used cotton and other natural fibers into a new, biodegradable raw material called Circulose® pulp. Here is how the technology works:
- Collect and sort textile waste: Renewcell works with textile recyclers, brands, and retailers to source used cotton-rich textiles and production waste. The textile waste is then collected, sorted, and shredded into small pieces.
- Dissolve the textile waste: The shredded textile waste is then dissolved in a chemical solution to break down the fibers and remove impurities. The solution is then filtered to remove any remaining impurities.
- Transform into Circulose® pulp: The filtered solution is then transformed into Circulose® pulp, which is a branded dissolving pulp made from 100% recycled textiles. The pulp is then dried into sheets and packaged into bales.
- Transform into regenerated fibers: The Circulose® pulp is then sold to fiber producers, who use it to make viscose, lyocell, modal, acetate, and other types of regenerated fibers. These fibers are then spun into yarns, woven or knitted into fabrics, and finally cut and sewn into new high-quality textile products.
The claimed positive points of Renewcell technology are:
- It provides a real alternative to high impact raw materials like cotton and polyester.
- Circulose® pulp is made from 100% textile waste, such as worn-out jeans and production scraps.
- The fiber is equal to or stronger than the virgin cotton or polyester it can replace.
- The technology is scalable and can be used to recycle large volumes of textile waste.
The limitations of Renewcell technology are:
- The chemical recycling process can be costly and often energy-intensive.
- The technology is still in the early stages of development and is not yet widely available.
- The process involves the use of chemicals, which may not be sustainable or environmentally friendly.
- There are extra costs included in pre-processing which comprises of washing, opening, separation process, removal of contaminations, decolour, etc.
Overall, Renewcell technology is a promising solution to the textile waste crisis, but it also has its limitations. The choice of chemicals and the conditions of the recycling process can impact the efficiency and environmental impact of the process.
Ioncell by Aalto
Ioncell technology is a chemical recycling process that turns used textiles, pulp, or even old newspapers into new textile fibers sustainably and without harmful chemicals. Here is how the technology works:
- Collect and sort textile waste: Ioncell works with textile recyclers, brands, and retailers to source used textiles and production waste. The textile waste is then collected, sorted, and shredded into small pieces.
- Dissolve the textile waste: The shredded textile waste is then dissolved in a non-toxic ionic liquid called 1,5-diazabicyclo[4.3.0]non-5-enium acetate ([DBNH]OAc) without co-solvents or stabilizers. The liquid dissolves the cellulose in the textile waste, leaving behind other materials like polyester.
- Transform into Ioncell fiber: The dissolved cellulose is then extruded through a spinneret to create new Ioncell fiber. The fiber is strong, even when wet, and has a silk-like feel to it. It reflects color very well and works well in both clothing and technical applications.
The claimed positive points of Ioncell technology are:
- It provides a real alternative to high impact raw materials like cotton and polyester.
- The Ioncell fiber is stronger than viscose and less of a burden on the environment.
- The fiber has a silk-like feel to it and reflects color very well.
- The technology is scalable and can be used to recycle large volumes of textile waste.
The limitations of Ioncell technology are:
- The chemical recycling process can be costly and often energy-intensive.
- The technology is still in the early stages of development and is not yet widely available.
- The process involves the use of chemicals, which may not be sustainable or environmentally friendly (although it is claimed that the used solvent in environmentally friendly).
- There are extra costs included in pre-processing which comprises of washing, opening, separation process, removal of contaminations, decolour, etc.
Overall, Ioncell technology is a promising solution to the textile waste crisis, but it also has its limitations. The choice of chemicals and the conditions of the recycling process can impact the efficiency and environmental impact of the process.
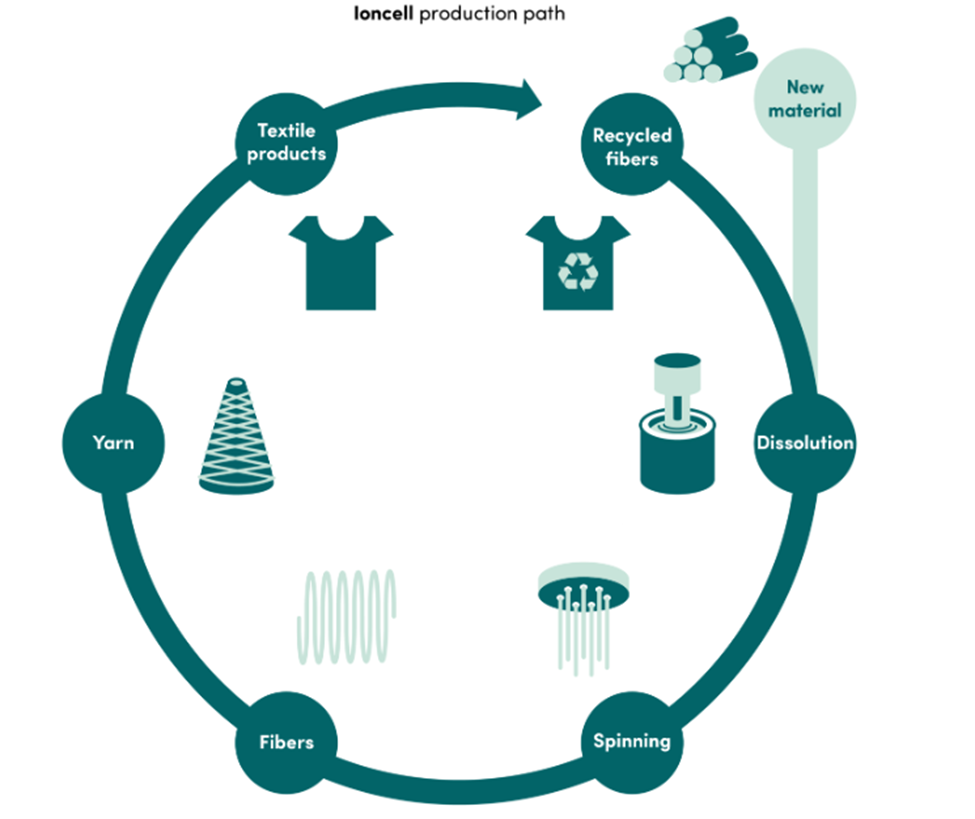
Refibra by Lenzing
Refibra technology by Lenzing is a closed-loop process for producing TENCEL™ Lyocell fibers from wood pulp and cotton scraps. Here is how the technology works:
- Collect and sort textile waste: Lenzing works with textile recyclers, brands, and retailers to source cotton scraps from garment production and other textile waste.
- Transform cotton scraps into cotton pulp: The cotton scraps are then transformed into cotton pulp using a mechanical and chemical process. The pulp is then mixed with wood pulp, which is sourced from sustainably managed forests.
- Transform into TENCEL™ Lyocell fibers: The combined pulp is then transformed into TENCEL™ Lyocell fibers using a closed-loop production process. The process involves dissolving the pulp in a non-toxic solvent, extruding the liquid into a new fiber, and then recovering and reusing the solvent.
The claimed positive points of Refibra technology are:
- It provides a real alternative to high impact raw materials like cotton and polyester.
- The technology uses pre-consumer cotton scraps and post-consumer garments from the textile value chain as raw materials.
- The fiber is equal to or stronger than the virgin cotton or polyester it can replace.
- The technology is scalable and can be used to recycle large volumes of textile waste.
- The technology is part of Lenzing’s commitment to sustainability and the circular economy.
The limitations of Refibra technology are:
- The chemical recycling process can be costly and often energy-intensive.
- The technology is still in the early stages of development and is not yet widely available.
- The process involves the use of chemicals, which may not be sustainable or environmentally friendly.
- There are extra costs included in pre-processing which comprises of washing, opening, separation process, removal of contaminations, decolour, etc.
Overall, Refibra technology is a promising solution to the textile waste crisis, but it also has its limitations. The choice of chemicals and the conditions of the recycling process can impact the efficiency and environmental impact of the process.
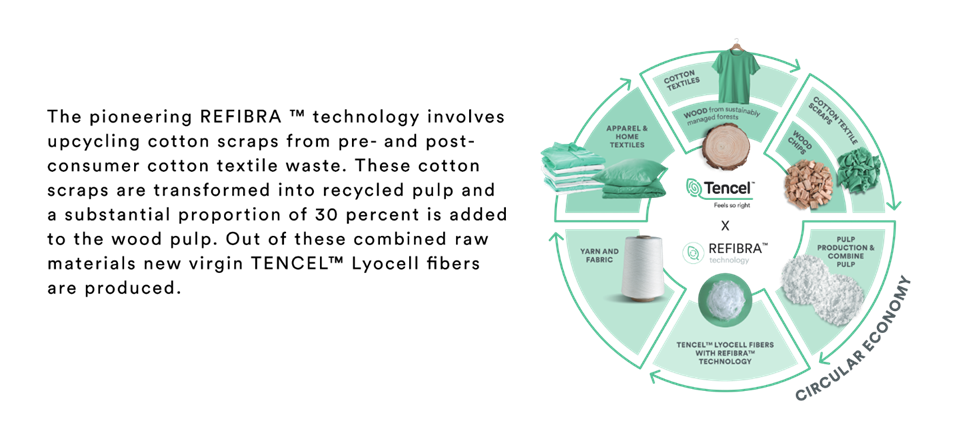
Saxcell Technology
Saxcell technology is a chemical recycling process that turns cotton waste into regenerated ‘virgin’ cellulose fiber. Here is how the technology works:
- Collect and sort cotton waste: Saxcell technology starts with sorting domestic cotton textile waste into an as pure as possible, well-defined waste stream. The sorting can be done by hand or mechanically.
- Transform cotton waste into cotton pulp: The cotton waste is then transformed into cotton pulp using a mechanical and chemical process. The pulp is then mixed with a non-toxic solvent that can dissolve cellulose.
- Transform into Saxcell fiber: The combined pulp and solvent are then transformed into Saxcell fiber using a spinneret. The fiber is strong, even when wet, and has a silk-like feel to it. It reflects color very well and works well in both clothing and technical applications.
The claimed positive points of Saxcell technology are:
- It provides a real alternative to high impact raw materials like cotton and polyester.
- The Saxcell fiber is stronger than viscose and less of a burden on the environment.
- The fiber has a silk-like feel to it and reflects color very well.
- The technology is scalable and can be used to recycle large volumes of cotton waste.
The limitations of Saxcell technology are:
- The chemical recycling process can be costly and often energy-intensive.
- The technology is still in the early stages of development and is not yet widely available.
- The process involves the use of chemicals, which may not be sustainable or environmentally friendly.
- There are extra costs included in pre-processing which comprises of washing, opening, separation process, removal of contaminations, decolour, etc.
Overall, Saxcell technology is a promising solution to the textile waste crisis, but it also has its limitations. The choice of chemicals and the conditions of the recycling process can impact the efficiency and environmental impact of the process.
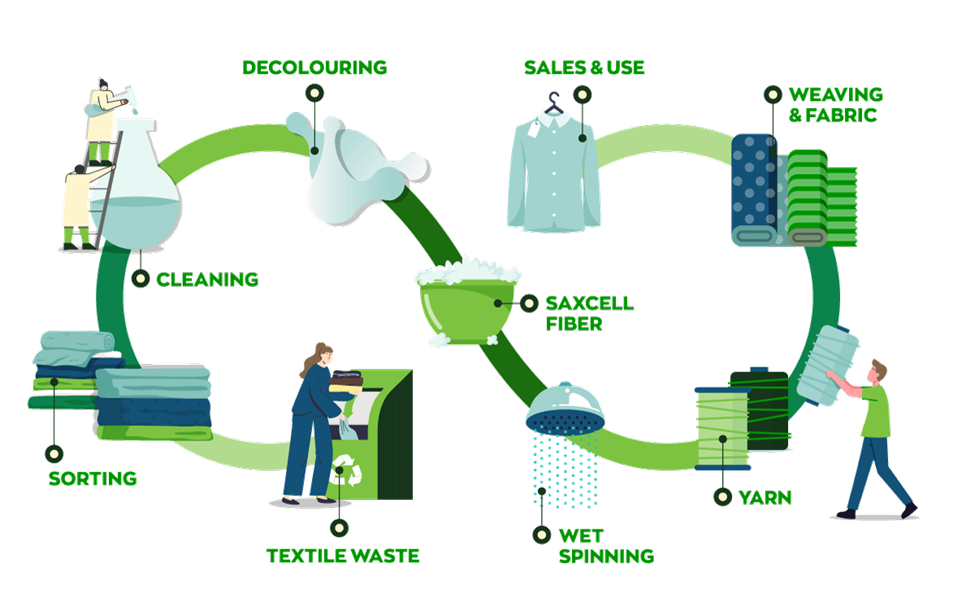
Infinited Fiber technology
Infinited Fiber is a textile recycling company that uses a patented technology to transform trashed textiles into brand-new premium-quality fibers for the textile industry. Here is how the Infinited Fiber technology works:
- Collect and sort textile waste: Textile waste is collected and sorted by type. The most valuable textiles for Infinited Fiber have a high cotton content.
- Disintegrate the textile waste: The textile waste is then disintegrated into small pieces using a mechanical and chemical process. The process removes non-cellulosic particles in the feedstock, such as polyester, elastane, and dyes.
- The cellulose is activated with urea and a stable, dissolvable cellulose carbamate powder is born.
- The cellulose powder is turned into a honey-like liquid and impurities are filtered out. New fiber filaments are born when the cellulose crystallizes during the wet spinning process.
- The fiber filament is cut, washed and dried. The regenerated cellulose carbamate staple fiber – Infinna™ – is ready for the next phase in the textile manufacturing supply chain.
The claimed positive points of Infinited Fiber technology are:
- It provides a real alternative to high impact raw materials like cotton and polyester.
- The Infinna™ fiber is strong, even when wet, and has a silk-like feel to it.
- The technology is scalable and can be used to recycle large volumes of textile waste.
- The fiber can be recycled with other textile waste and reborn again as Infinna™.
The limitations of Infinited Fiber technology are:
- The chemical recycling process can be costly and often energy-intensive.
- The technology is still in the early stages of development and is not yet widely available.
- The process involves the use of chemicals, which may not be sustainable or environmentally friendly.
- There are extra costs included in pre-processing which comprises of washing, opening, separation process, removal of contaminations, decolour, etc.
Overall, Infinited Fiber technology is a promising solution to the textile waste crisis, but it also has its limitations. The choice of chemicals and the conditions of the recycling process can impact the efficiency and environmental impact of the process.
1
Chemical recycling | Mechanical recycling | |
Length of waste fibers | not important | important |
Composition of waste fibers | separation needed to obtain cellulose with a high purity | yarn spinning is effected by composition |
Quality of produced fibers | high | low/medium |
Color of produced fibers | white | depends on the waste |
Products with 100% recycled fibers possible? | yes, high value | no, (lower value) |
Costs | medium/high | low/medium |