Denim is one of the most popular and versatile fabrics in the world, but it also has a huge environmental impact. From the water and chemicals used to grow cotton and dye the fabric, to the energy and waste generated by the production process, denim is responsible for a lot of pollution and resource depletion.
But what if there was a way to make denim more sustainable, without compromising on quality, style, or affordability? That’s the mission of Crescent Bahuman Limited (CBL), a leading denim manufacturer based in Pakistan. Crescent Bahuman is committed to producing denim that is not only durable and fashionable, but also environmentally and socially responsible. In this article, we will see some of their sustainable innovations and initiatives.
What is responsible denim manufacturing?
Responsible denim manufacturing is a term that encompasses various practices and technologies that aim to reduce the environmental and social impacts of denim production. Some of these practices include:
- Using organic or recycled cotton, which requires less water, pesticides, and fertilizers than conventional cotton.
- Using natural or low-impact dyes, which are less toxic and harmful to the workers and the environment than synthetic dyes.
- Using water-efficient washing and finishing techniques, which minimize water consumption and wastewater generation.
- Using renewable energy sources, such as solar or wind power, to power the factories and reduce greenhouse gas emissions.
- Implementing waste management and recycling systems, which prevent landfilling and incineration of textile waste and promote circular economy principles.
- Ensuring fair wages, safe working conditions, and social benefits for the workers and the communities involved in the denim supply chain.
How does Crescent Bahuman practice responsible denim manufacturing?
Crescent Bahuman is one of the pioneers of responsible denim manufacturing in Pakistan and beyond. The company was founded in 1995 as a joint venture between Greenwood and Crescent Group, a leading textile conglomerate in Pakistan. In 2001, it became completely owned by Crescent and renamed as – Crescent Bahuman Limited. Since then, Crescent Bahuman has grown to become one of the largest vertically integrated denim manufacturers in the world.
Crescent Bahuman has also invested heavily in sustainability initiatives across its operations. Some of the highlights include:
- Using better cotton and organic cotton from certified sources, such as Better Cotton Initiative (BCI) and Global Organic Textile Standard (GOTS).
- Using natural indigo dye from Indigofera Tinctoria, which is derived from plants and has no synthetic chemicals or additives.
- Using laser technology for distressing and whiskering effects, which eliminates the need for manual sandblasting or chemical spraying.
- Using ozone technology for bleaching and fading effects, which reduces water consumption by up to 90% and eliminates the use of chlorine or potassium permanganate.
- Using nano-bubble technology for washing and softening effects, which reduces water consumption by up to 80% and enhances fabric quality and durability.
- Using solar panels to generate 2.5 MW of electricity per day, which covers 25% of the factory’s energy needs.
- Implementing a zero liquid discharge (ZLD) system, which treats and recycles all wastewater generated by the factory, leaving no effluent discharge.
- Implementing a waste-to-energy (WTE) system, which converts textile waste into biogas that can be used for heating or power generation.
- Implementing a social compliance program, which ensures compliance with international labor standards, such as SA8000, WRAP, BSCI, SEDEX, etc.
Some Sustainable Innovations and Initiatives by Crescent Bahuman
- Blue Infinity: This is a new technology that allows Crescent Bahuman to create a range of blue shades with low environmental impact. Dyeing is performed, taking indigo out of the dyeing process, in a compact dyeing range using only a small number of boxes for the whole process, reducing the total volumes of required water. Blue Infinity reduces water consumption up to 70%, energy consumption up to 50%, and chemical consumption up to 90%. It also improves fabric quality and durability, as well as worker health and safety.
- Cleankore: This is a patented technology that enables Crescent Bahuman to produce denim with a clean and smooth surface, without using any harmful chemicals or processes. Cleankore uses a special yarn that has a core of polyester and a sheath of cotton. The polyester core prevents the cotton sheath from absorbing the indigo dye, resulting in a clean white core that contrasts with the blue surface. This creates a unique visual effect that can be enhanced by different washes and treatments. Cleankore reduces water consumption by 50%, energy consumption by 40%, and chemical consumption by 80%. It also improves fabric quality and comfort.
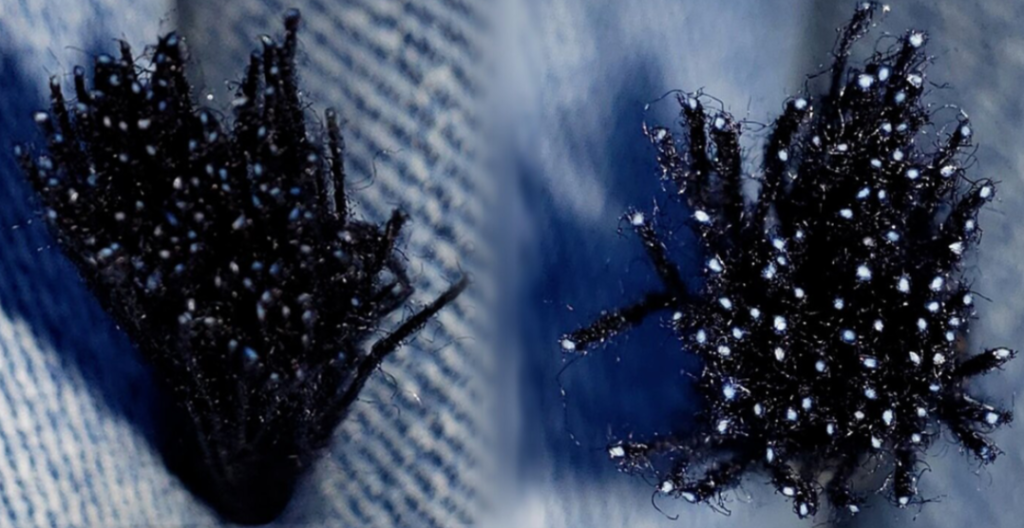
- Dyneema® Denim: This is a technology that allows Crescent Bahuman to produce denim with exceptional strength and durability, without compromising on style or comfort. Dyneema® is a high-performance fiber that is 15 times stronger than steel and 40% lighter than aramid fibers. By blending Dyneema® with cotton, Crescent Bahuman creates denim that can withstand abrasion, tearing, and puncturing, while maintaining softness and breathability. Dyneema® Denim is ideal for protective clothing, such as motorcycle jeans or workwear.
- Smart Factory 4.0: This is a digital transformation project that aims to improve the efficiency, transparency, and intelligence of Crescent Bahuman’s operations. The project involves connecting all the machines, processes, and data in the factory through a single dashboard, which provides real-time information and insights on various metrics, such as production, quality, energy, water, waste, etc. The project also enables better decision making, problem solving, and optimization of resources and performance.
- PaperTale: This is a blockchain-based tracing technology that enables Crescent Bahuman to provide full transparency and traceability of its products and processes. PaperTale uses NFC tags that can be scanned by any smartphone, which reveals the entire supply chain map of the product, from the raw material to the finished garment. PaperTale also shows the environmental and social impacts of the product, such as the carbon footprint, water footprint, recycled content, fair wages, etc.
- A Lighter Touch: This is a new product collection that showcases Crescent Bahuman’s expertise in creating lightweight denim fabrics with high performance and comfort. The collection uses organic cotton, recycled polyester, hemp, and Tencel fibers, as well as natural indigo dye and water-efficient washing techniques. The collection offers a variety of styles, fits, washes, and treatments that appeal to different markets and consumers.
- Naya Denim: This is a new indigo-dyeing process that uses precision technology to save water, energy, and chemicals. Naya Denim reduces water consumption by 99.5% at the dyeing stage, and another 80% at the finishing stage. It also reduces energy consumption by 50% and chemical consumption by 90%. Naya Denim has been audited and validated by TUV Rheinland, a quality assurance service provider.
- Our Ecosystem: This is a project that documents Crescent Bahuman’s 25-year-long quest of creating the greenest ecosystem in the denim industry. The project showcases the company’s achievements and challenges in various aspects of sustainability, such as water management, energy management, waste management, social compliance, etc. The project also highlights the company’s vision and goals for the future.
- Echo Sustainable Stone Washing (EESW): This is a technology that uses natural enzymes to create stone washing effects on denim garments, without using any stones or chemicals. EESW reduces water consumption by 50%, energy consumption by 40%, and chemical consumption by 80%. It also improves fabric quality and comfort, as well as worker health and safety.
- Delta System Washing: This is a technology that uses high-pressure water jets to create different washes and treatments on denim garments, without using any chemicals or abrasives. Delta System Washing reduces water consumption by 70%, energy consumption by 50%, and chemical consumption by 90%. It also improves fabric quality and durability, as well as worker health and safety.
- Less Water Quick Drying (LWQD): This is a technology that uses a low liquor ratio of 1.5 liters of water per 1 kg of apparel to dye and finish denim fabrics, without compromising on color fastness or quality. LWQD reduces water consumption by 80%, energy consumption by 50%, and chemical consumption by 90%. It also improves fabric quality and performance, as well as worker health and safety.
- Environment Impact Measuring (EIM): This is a software that measures the environmental impact of denim production processes and inputs, such as water, energy, chemicals, etc. EIM helps Crescent Bahuman to quantify and communicate its sustainability initiatives and achievements, as well as to identify areas for improvement and optimization.
- Spray Silicon and Softener (SILK): This is a technology that uses spray nozzles to apply silicon and softener on denim garments, without using any water or chemicals. SILK reduces water consumption by 100%, energy consumption by 50%, and chemical consumption by 90%. It also improves fabric quality and comfort, as well as worker health and safety.
- Organic Bleach: This is a technology that uses hydrogen peroxide to bleach denim fabrics, without using any chlorine or other harmful chemicals. Organic Bleach reduces water consumption by 50%, energy consumption by 40%, and chemical consumption by 80%. It also improves fabric quality and color, as well as worker health and safety.
- KMNO4-Free Spray: This is a technology that uses ozone gas to create fading effects on denim garments, without using any potassium permanganate or other harmful chemicals. KMNO4-Free Spray reduces water consumption by 90%, energy consumption by 50%, and chemical consumption by 90%. It also improves fabric quality and durability, as well as worker health and safety.