Rising energy costs are hitting the textile industry hard, especially for yarn manufacturers. With global energy prices surging and environmental regulations tightening, the pressure on spinning mills to reduce costs while maintaining quality has never been greater. Traditional spinning methods consume excessive amounts of energy, cutting into profit margins and worsening environmental impacts. This is where Saurer’s Autocoro 11 steps in—a revolutionary rotor spinning machine designed to dramatically lower energy consumption, reduce operational costs, and align with sustainability goals.
The Cost Challenge in Yarn Production
For spinning mills, the cost of yarn production is increasingly driven by energy expenses. Energy ranks as the second-largest cost, just behind raw materials. In a highly competitive global market, controlling these costs is essential for profitability. Yet, many spinning mills still rely on older, energy-inefficient machinery, which inflates their operational costs and contributes to excessive energy consumption.
With growing economic, political, and financial pressures, finding a solution that tackles energy consumption is no longer optional—it’s a necessity. Spinning mills are looking for ways to cut costs without sacrificing product quality or sustainability. The Autocoro 11, by Saurer, addresses this exact problem.
Autocoro 11: Setting a New Standard in Energy Efficiency
The Autocoro 11 stands out in the world of rotor spinning as the machine with the lowest energy consumption on the market. It integrates advanced technology to deliver economic and environmental benefits, making it a top choice for spinning mills aiming to future-proof their operations.
Here’s how it does it:
Revolutionary Extraction System:
- One of the biggest energy drains in traditional spinning is the vacuum system, which accounts for 30% of energy usage. The Autocoro 11 features a completely redesigned extraction system, boosting efficiency by up to 85%. This new system precisely adjusts the suction air based on each process’s needs, such as yarn searching and spinning, eliminating the wasteful “one-size-fits-all” approach of older systems.
Energy-Optimized Winding Device:
- Another key innovation is the winding device, which consumes substantial energy to handle and wind tonnes of yarn annually. With cutting-edge energy-efficient drives, Saurer has significantly reduced the base load of this component.
Comprehensive Electronic Energy Optimization:
- All electronic components in the machine, from power supply units to sensors, have been thoroughly optimized to reduce energy consumption. This results in a streamlined, efficient system that operates at 10% lower energy usage compared to the previous generation, and up to 48% lower energy consumption than older rotor spinning machines still in use.
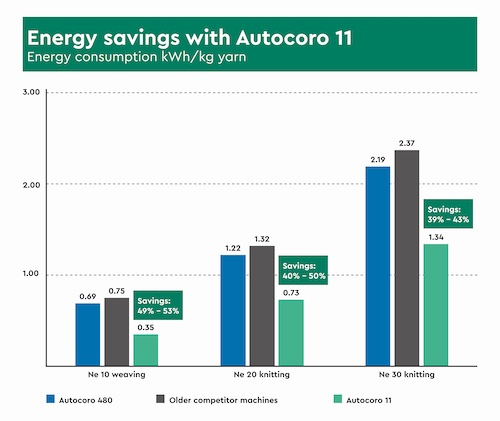
Figure 1: Energy savings with the Autocoro 11 in kWh/kg yarn © 2024 Saurer
Tangible Savings: The Financial and Environmental Impact
The Autocoro 11 offers substantial cost savings for spinning mills. Even in areas with moderate energy prices, the energy cost reductions achieved by this machine can reach six figures annually for a single machine with 480 spinning positions.
For example, at an energy cost of €0.10 per kWh, the savings are remarkable. This makes a significant difference for spinning mills operating in regions with fluctuating or rising energy costs. And it’s not just about the bottom line—reducing energy usage also supports environmental sustainability.
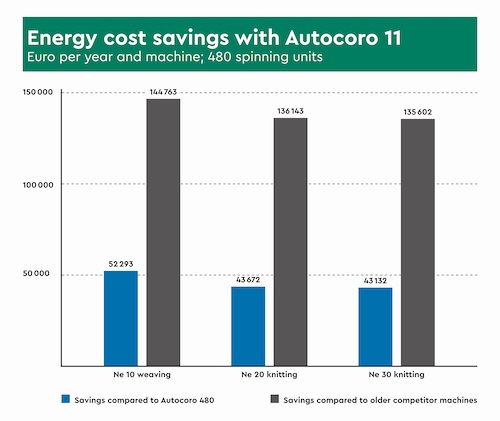
Figure 2: Annual cost savings with 480 spinning positions © 2024 Saurer
- Up to 48% Energy Savings: Compared to older machines, the Autocoro 11 cuts energy consumption by nearly half, which translates to a significant reduction in greenhouse gas emissions.
- Additional Savings Potential: By fine-tuning spinning settings—such as reducing the vacuum, increasing rotor speed, and using smaller rotors—further energy reductions are possible, potentially delivering a double-digit percentage drop in energy consumption. This customization allows mills to optimize operations based on specific raw materials and yarn quality demands.
Contributing to Global Sustainability Goals
Beyond the financial benefits, the Autocoro 11 plays a crucial role in achieving sustainability targets. As industries worldwide strive to lower their carbon footprints, reducing energy consumption in industrial processes is key. The textile industry, a known contributor to environmental issues, is under increasing pressure to adopt climate-friendly solutions.
- Solar-Powered Spinning Mills: Several forward-thinking mills have already begun using renewable energy, such as solar panels, to power their Autocoro spinning machines. This not only reduces reliance on grid energy but also ensures that the production process is climate-neutral, contributing to broader global climate goals.
Innovation That Meets Modern Challenges
The Autocoro 11 is not just about cost savings—it’s about enabling yarn producers to meet the challenges of the future. As demand for eco-friendly production practices increases, businesses using outdated, energy-guzzling equipment will struggle to compete.
The Autocoro 11 aligns perfectly with the modern demands for sustainability, efficiency, and profitability. Its innovations allow mills to:
- Reduce operational costs, making production more competitive.
- Improve their environmental credentials, aligning with consumer and regulatory expectations.
- Remain future-proof, with machinery designed to last and evolve with the industry’s sustainability needs.
Conclusion: A Must-Have for Forward-Thinking Spinning Mills
As the textile industry navigates a rapidly changing landscape, marked by rising energy costs and growing environmental responsibilities, the Autocoro 11 offers a clear solution. By drastically reducing energy consumption, providing flexible, sustainable options, and delivering massive cost savings, it enables spinning mills to thrive in this new era of textile production.
For any spinning mill looking to cut costs, boost efficiency, and meet the increasing demands for sustainability, the Autocoro 11 is not just a smart investment—it’s a necessary one. The future of yarn production lies in energy-efficient technologies, and the Autocoro 11 is leading the way.